Facilities
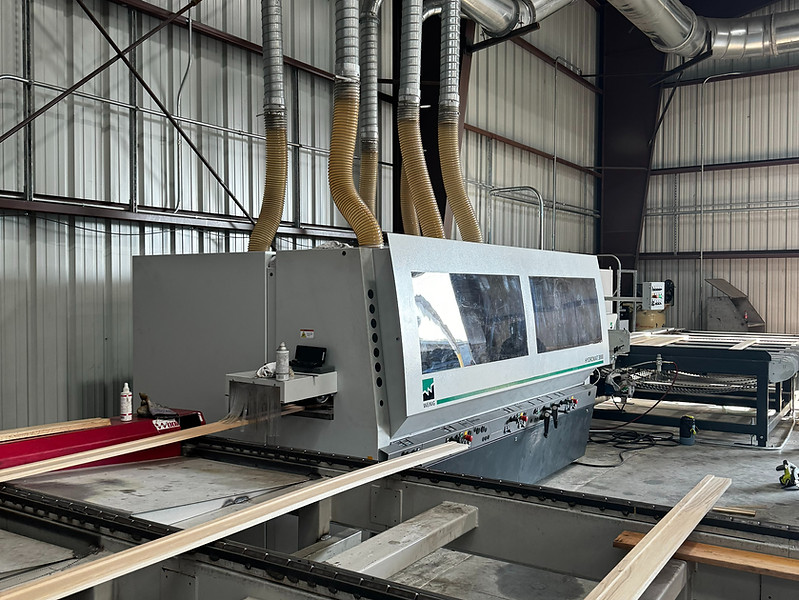
Facilities
Line 5
Line 5 is the newest addition to our facilities. Here we operate a brand new Weining Hydromat 3000 that takes gang ripped lumber from our various lines and transforms it into S4S, tongue and grove, crown moulding, case and base, stair parts, and other profiles.
This production line has capabilities for quick shift in profiles and can run180 LF per minute.
​
This line comes equipped with a state-of-the-art R1000 CNC profile grinder.
​

Line 1
Our line 1 is comprised of state of the art equipment from LICO. We have a Newman S-382, a Lucidyne 3D Scanner, an end trim saw, a high speed optimized gang rip saw and a finishing planer all in sync to serve you.
Classic American Hardwoods is proud to boast technology, for you, that is mostly superior to the industry. The technology has allowed us to be extremely efficient, moving 120,000 board-feet per day, but most importantly, accurate.
With less labor invested into our lumber, we are able to produce exactly what you and your customer need as efficiently and accurately as possible.
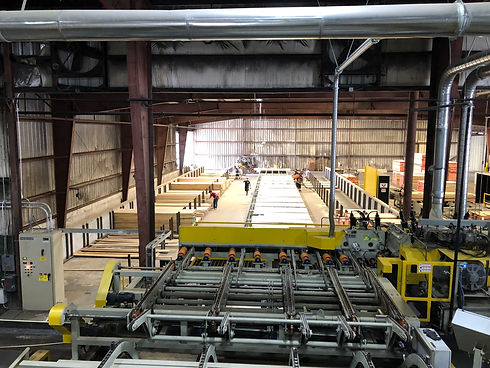
48 Stacking Bays
Each lumber puller pulls into one of our 48 stacking bays. Having so many allows for all types of sorting in order to accommodate our customers diverse needs.

Line 2
Line two is our secondary kiln dried grading line that has an inline Newman 382 roughing planer with a 36 bay sorting chain behind it.
We perform various proprietary grades, widths sorts and color sorts to help supplement our Line 1 grading system.
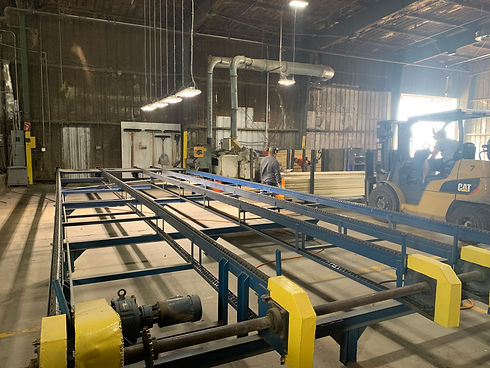
Line 3
Line 3 is our in-house small finish mill that includes a Straight Line rip machine and Newman 970 2 sided helical head Finish planer.
We support customers with value added finish capabilities whether it is S2S finish thickness or SLR milling to our kiln dried lumber.
All production items are packaged with cardboard toppers to protect milled edges while in transport to our customers.

Line 4
Line 4 is our secondary planer and ripping mill that additionally supports our main optimized ripping system.
On this line we operate a Mereen Johnson fixed arbor gang rip machine with 5 pocket ripping capabilities and a Newman 282 roughing planer for additional planning capabilities.
Our unique combo pull chain setup allows us to rip and surface lumber at the same time to a single pull chain allowing for increase production in a limited footprint.

Green Yard
Green lumber shipments are received daily on flat bed trucks into our green lumber yard which is location next to our two green lumber stackers. Here, lumber is stored until it is scheduled to be stacked and then placed on the air drying yard. Our green yard has the capacity to store 700,000 board-feet of green lumber and to stack 120,000 board-feet per day.

Kilns
Once lumber has reached the proper moisture content on the air drying yard, it is placed in one of our 16 kilns. We optimize drying capacity through the use of eight package kilns and eight track kilns, totaling a drying capacity of 1,000,025 board-feet. All 16 kilns are powered using two 300 horsepower fire tube boilers. The boilers are fueled through the collection of dust from all millwork operations on the plant.

Boiler Room
The boilers are used to create steam through burning sawdust to heat water to create steam. All of the energy needed to heat the boilers comes from our millwork through dust collection systems. The two 300 Horsepower boilers are capable of providing sufficient heat to all of our 16 dry kilns.

Additional Machinery
-
S382 primary roughing planer
-
Optimized 3D scanner
-
Only company in the WORLD to have this software ​
-
Reads every board accurately up to 1/64th of an inch
-
-
LICO double ended trim saw
-
High speed rip saw​
-
Secondary S282 planer
-
Allows ripped product to be surfaced on line ​
-
-
Matthews Ink jet marking system
-
Prints grade on top of board, each end​
-
Eliminates paint booth
-
-
48 Bay sorting line
-
Handles all- rough, surfaced, width sorted, color sorted, gang ripped and straight line ripped product combinations​
-
-
Vision Tally with inline scale
-
Extreme precision laser tallying system​
-
-
Fromm automatic banding machine
-
Weining Hydromat 3000